Spare parts for hot and cold rolled rolling mills
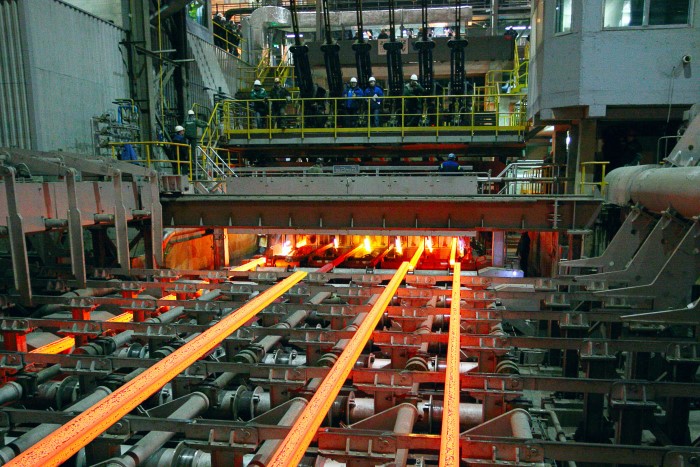
Benches and rolling mills.
Rolling mills are equipment for metal processing by rolling. They are used in the metallurgical industry to produce various metal products such as sheets, strips, profiles and pipes.
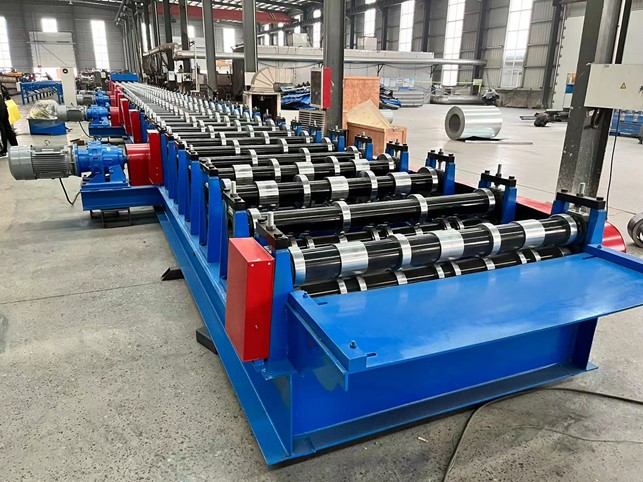
Types of rolling mills:
Plate mills – designed for the production of metal sheets and strips.
Profiling mills – used for the manufacture of metal profiles of various cross-sections.
Pipe rolling mills – used for the production of metal pipes.
Multilayer rolling mills – includes several rolling mills working in series to achieve the required shape and size metal
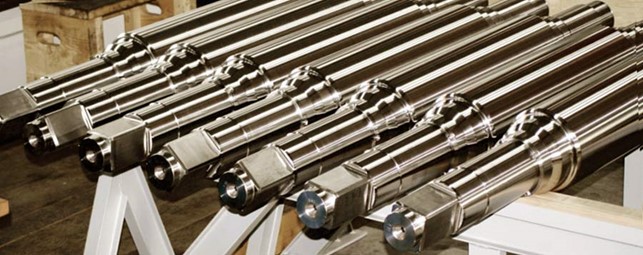
Forged support and working rolls.
Support rolls
Purpose: Support rolls support working rolls and accept the main load of the rolling process.
Materials: Made of high-strength steels and alloys that have high wear resistance and mechanical stress.
Manufacturing process: Forged support rolls are manufactured by forging method, which ensures high material density and minimum defects.
Application: Used in various types of rolling mills including hot and cold rolling.
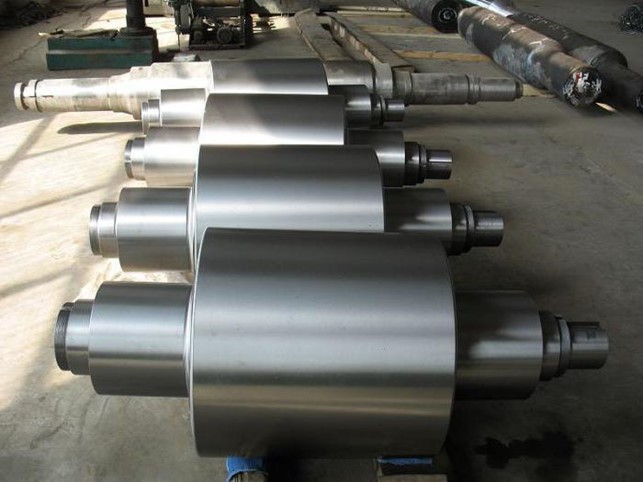
Working rollers
Purpose: The working rolls are in direct contact with the metal, giving it the desired shape and size.
Materials: Made of high alloy steels that have high hardness and wear resistance.
Manufacturing process: Forged working rolls pass through the forging, quenching and heat treatment process to achieve the required hardness and durability.
Application: Widely used in rolling mills for the production of sheets, strips, profiles and pipes.
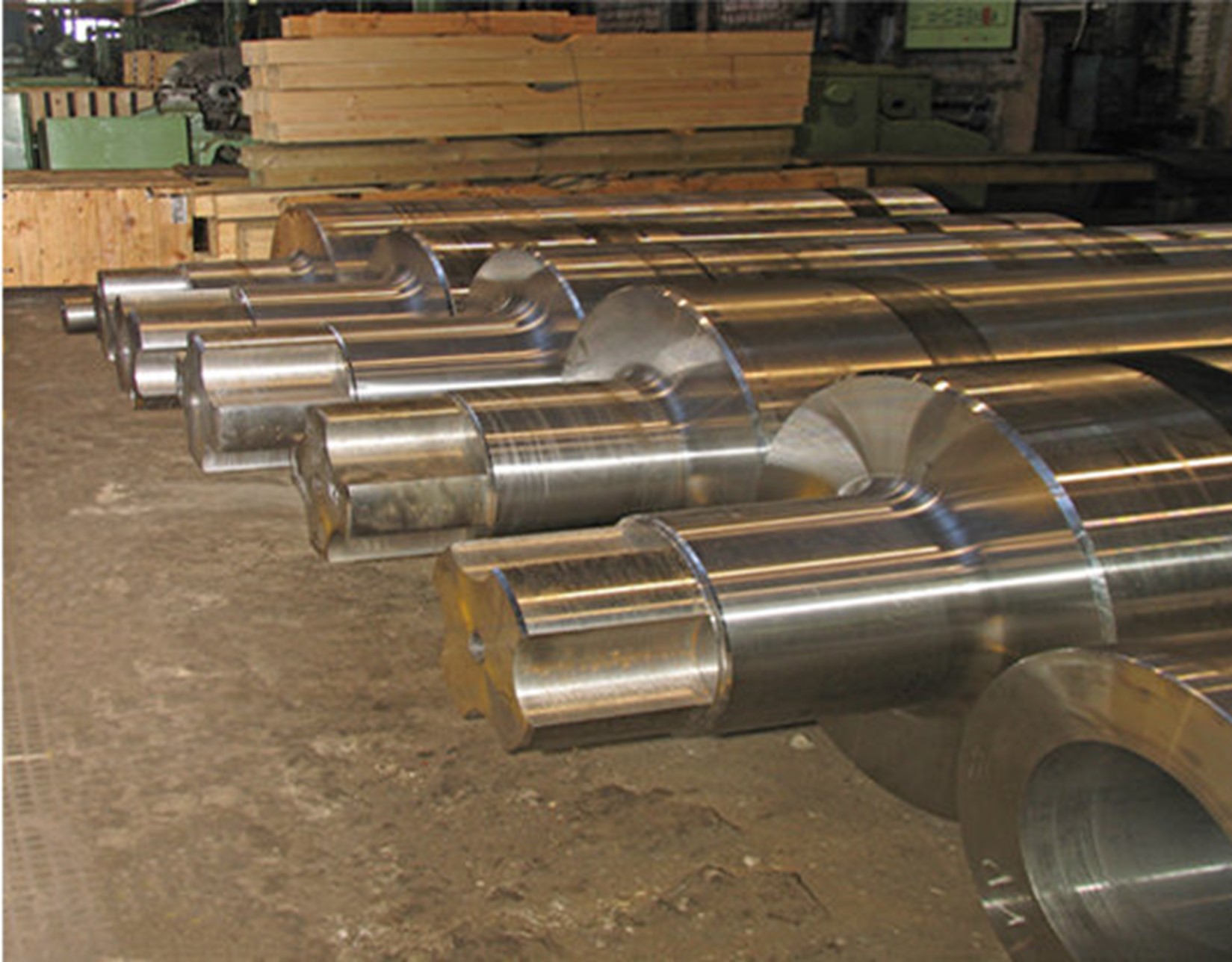
Cast support and working rolls.
Cast support and working rolls play an important role in rolling stock production, offering cost-effective and flexible solutions for a variety of applications. However, compared with forged rolls, they can have drawbacks in strength and wear resistance, which requires careful choice of material and production technology depending on the specific operating conditions.
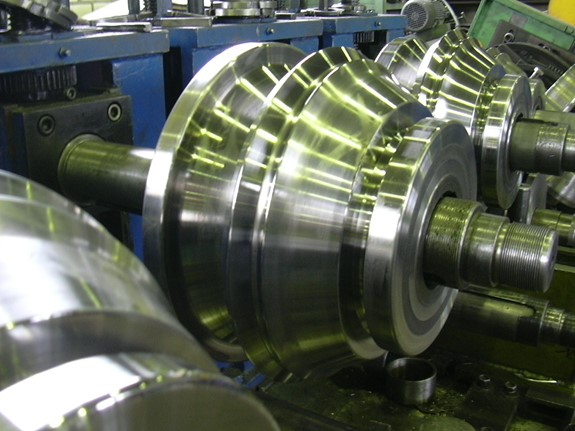
Other rolls for rolling construction steel rails.
Other rolling rolls for structural steel rails include black, intermediate and finish rolls, each with its own role in the rail profile forming process. These rolls are made of high-strength materials and have special design features to ensure the accuracy, strength and durability of the rolling parts.
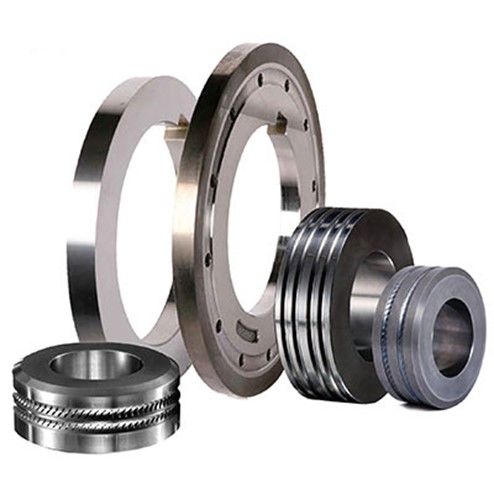
Ceramic rollers and carbide rings.
Ceramic rollers
Purpose: Ceramic rollers are used in rolling mills for processing various metal products, providing high precision and surface quality.
Materials: Made of technical ceramics such as aluminum oxide or silicon nitride, with high hardness and wear resistance.
Application: Used in high precision rolling operations where it is necessary to minimize surface defects and high purity of processing.
Carbide rings
Purpose: Carbide rings are used in rolling rolls to increase their strength and durability, especially in conditions of high load and intense wear.
Materials: Made from tungsten carbide, titanium carbide and other carbides, providing high hardness and wear resistance.
Application: Used in heavy duty rolling mills, especially in the manufacture of metal products where precision and durability of the tool are important.
Ceramic rollers and carbide rings are important components in the rolling industry. Ceramic rollers provide high precision and wear resistance when processing metals, while carbide rings increase the life of rolls and increase the efficiency of rolling mills under high load conditions.
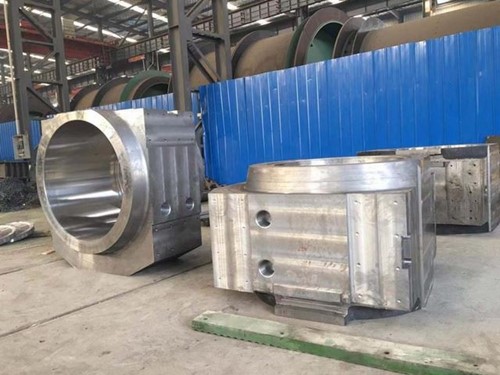
Housing and bearing units
Purpose: Bearing housings are used to install and protect bearings, ensuring their correct position and performance in various mechanisms.
Materials: Made of cast iron, steel, aluminum alloys or composite materials providing strength and corrosion resistance.
Types of casings:
Flanged housing: Has a flange for fixing to a flat surface.
Paw housing: Equipped with legs for attachment to the base.
Detachable housing: Consists of two halves, which facilitates the mounting and dismantling of bearings.
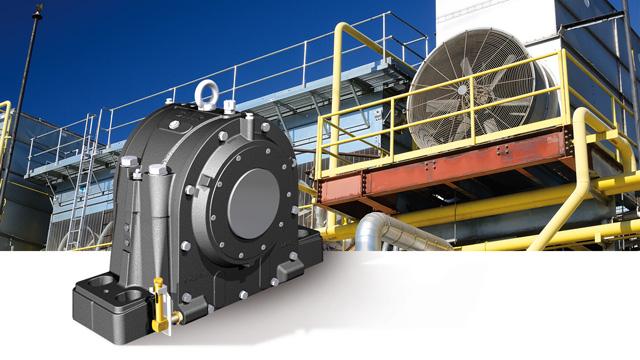
Bearing units
Purpose: Bearing units are ready-to-install modules consisting of housing and integrated bearing. They simplify the process of mounting and servicing bearings in the equipment.
Materials: Bearing block housings can be made of the same materials as individual bearing housings, and the bearings themselves are usually made of high-strength steel.
Types of bearing units:
Plate Blocks: Have a flat plate for fixing to the base.
Support units: Have a base for installation on a support or frame.
Sealing units: Equipped with additional seals to protect the bearings from dirt.
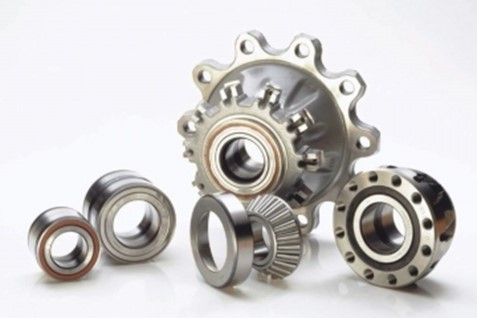
Liquid Friction Bearings (LFB).
Purpose: Liquid friction bearings are used to support and reduce friction between moving parts of the mechanisms by creating a thin film of liquid between the surfaces.
Operating principle: The movement of shafts or other components creates a hydrodynamic pressure that forms a thin layer of fluid (oil, water or other lubricant) between the bearing and shaft. This liquid layer prevents direct contact with metal surfaces, reducing wear and friction.
Application: Widely used in turbomachines, pumps, compressors, large electric generators and other high-speed and high-load mechanisms where high accuracy and reliability of operation is required.
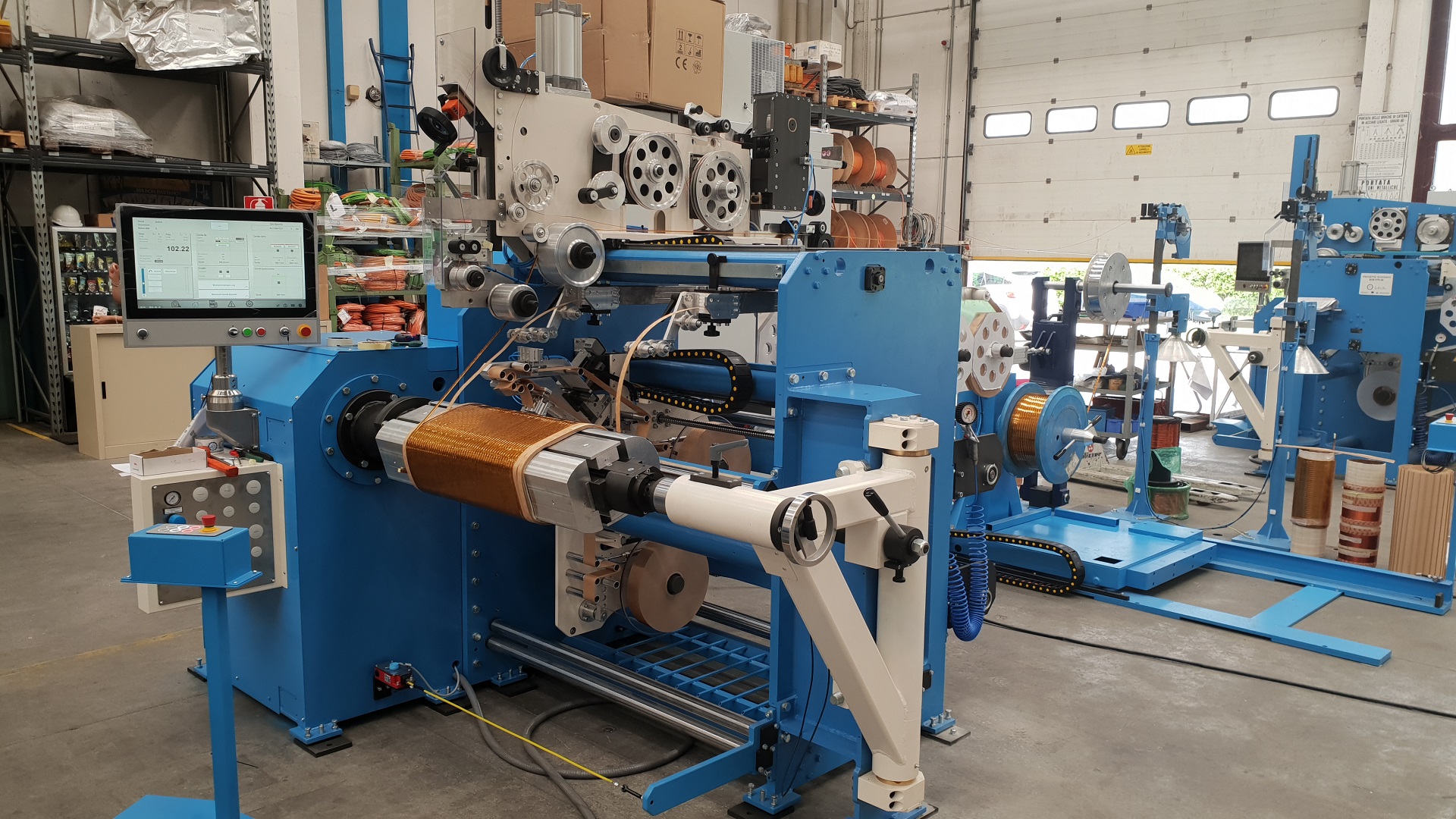
Coils and winding devices
Coil
Purpose: Coils are used for storage and transportation of long materials such as wire, cable, tape, threads and other flexible materials.
Reel Types:
Industrial coils: Used for heavy and large materials.
Electrotechnical coils: Used for winding cables and wires in the electrical industry.
Textile coils: Used for the winding of threads and yarns in the textile industry.
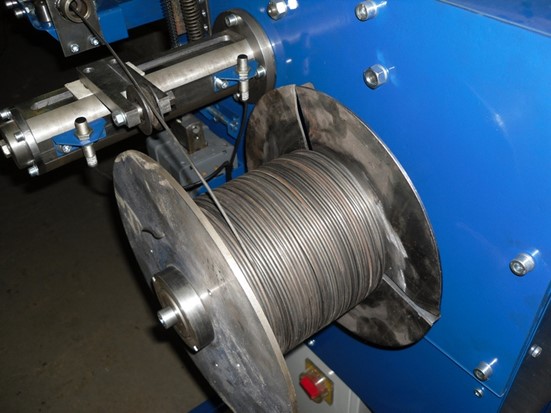
Winding devices
Purpose: Winding devices are designed to automate the process of winding materials to coils or spools, ensuring uniform and accurate material distribution.
Types of winding devices:
Mechanical winding devices: Manually or mechanically operated.
Electrical winding devices: Use electric motors for winding material, often equipped with automatic control systems.
CNC winding devices: Equipped with numerical program control (CNC) for high precision and winding automation.
Coils and winding devices are important components in various industries, providing easy storage, transportation and use of long materials. The coils allow for gentle and compact storage of materials, and the winding devices automate the winding process, ensuring accuracy and efficiency.